Переставили станки — и поставили личный рекорд. Разбираем кейс оптимизации производства
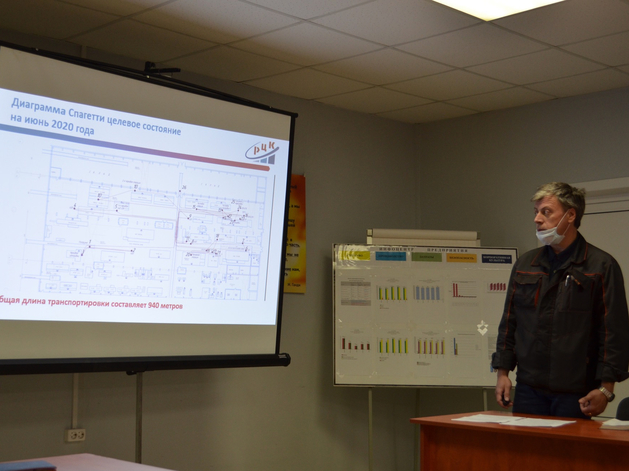
Нацпроект уже повысил эффективность у нескольких десятков производственных компаний Свердловской области. В ближайшие четыре года производительность труда повысят еще три сотни предприятий.
Представители Регионального центра компетенций утверждают: увеличить выработку на предприятии на 30% вполне реально без дополнительных инвестиций, модернизации оборудования и поиска новых сотрудников. Достаточно сократить существующие издержки, стандартизировать процессы и внедрить принципы бережливого производства. Звучит, как сказка, однако специалисты Регионального центра компетенций, который уже полтора года реализует в регионе нацпроект «Производительность труда и поддержка занятости», могут привести десятки примеров такого «сказочного» преображения предприятий. Для спецпроекта DK.RU они разобрали кейс работы с ЗАО «Кушвинский завод прокатных валков». За пять месяцев оптимизации всего одного участка удалось добиться значительного роста производительности целого цеха. А дальнейшее тиражирование полученного опыта на весь завод позволит вывести предприятие на новый уровень, увеличить объем выпуска и повысить качество продукции, расширить количество и географию клиентов.
Компания: ЗАО «Кушвинский завод прокатных валков», который изготавливает и поставляет прокатные валки для листопрокатных и сортопрокатных станов, ролики для трубопрокатных станов, бандажи для строительной индустрии и металлургической промышленности. На заводе работает около 650 человек.
В последние годы предприятие неоднократно обновляло свой производственный парк и расширяло номенклатуру продукции, которая востребована как в России, так и за рубежом. В марте этого года в эксплуатацию был запущен обрабатывающий центр по производству крупных валков массой свыше 30 тонн, а в ближайшие годы на предприятии планируют запустить производство валков массой до 75 тонн.
Спрос на продукцию завода растет быстрее производительности труда, что грозит просроченными контрактами, возможной потерей клиентов, репутационными рисками и штрафами. Поэтому для предприятия очень важно оптимизировать процессы, чтобы производить продукцию не только качественно, но и в тех объемах и в те сроки, которые требуют от него потребители.
Цель: Повысить производительность труда
Задачи:
- снизить объем незавершенного производства;
- уменьшить объем брака;
- увеличить ежемесячную выработку на одного сотрудника;
- сократить время на производственные процессы и уменьшить процент простоя оборудования.
Что мы делали:
Для начала мы познакомились с вальцеделательным производством и на совместном совещании с представителями завода выбрали участок, который в наибольшей степени нуждался в оптимизации — участок черновой обработки прокатных валков в вальцемеханическом цехе. Поскольку он находится в начале цепочки переделов, его простои негативно сказывались на деятельности других участков.
Оптимизировали эргономику производственного участка
Мы сделали диаграмму спагетти (графическое отражение перемещений работника) и поминутный хронометраж действий сотрудников цеха и выяснили, что во многом низкая производительность связана с плохой эргономикой участка. Из-за нее время на производственные процессы неоправданно увеличивается, оборудование простаивает (до 8% от общего фонда рабочего времени оборудования цеха), скапливается большой объем незавершенного производства.
Чтобы решить эту проблему, мы изменили расстановку объектов в цехе: на 25 метров перенесли заточный станок, на 180 метров — участок слесарных работ и маркировки.
Результат: если в феврале общая дистанция транспортировки изделия по цеху составляла 1120 метров, то в июне она составила 940 метров. Это сократило время производственных операций, снизило объем НЗП и время простоя оборудования.
Когда мы оценили процесс перемещения валков по цеху методами, предложенными представителями РЦК, мы наглядно увидели, как много перемещений и непроизводительной работы совершаем. В итоге перенесли участок маркировки валков и приемки ОТК, а также заточной станок: конфигурация цеха со временем менялась, и по оставшимся рабочим местам до станка было ходить далеко, — рассказывает начальник вальцемеханического цеха Дмитрий Шавриков.
Внедрили принципы бережливого производства и стандарты 5С на рабочем месте
Анализ работы на этом участке показал, что процесс тормозит большое количество разнообразных неудобств. Некоторые вызваны объективными причинами и требуют временных и денежных затрат — например, установка нового оборудования для отгрузки на склад валков весом свыше 30 тонн, закупка нового инструмента и расходников, повышение квалификации станочников. Безусловно, со временем эти вопросы будут решены. Но интересно, что значительную часть проблем можно устранить без каких-либо вложений с помощью стандартизации процессов. Например, в цехе не хватает стеллажей для хранения, у сотрудников нет привычки поддерживать чистоту на рабочих местах, полуфабрикаты и готовая продукция хранятся в одном месте, нет места под ОТК. Доходит до смешного: нет емкостей под металлическую стружку. Все это приводит к тому, что производительность труда снижается, а количество брака и простоев — растет.
Мы помогли рационально организовать рабочее место, прописали стандарт его уборки, передачи другому сотруднику. Регламентировано было все, вплоть до обращения тары из-под стружки.
В результате у сотрудников значительно сократилось количество непродуктивных рабочих действий. А то, что их было много, стало понятно после составления хронометража рабочего времени, по которому, например, было видно, сколько времени терял рабочий на поход в кладовую за режущей пластиной, которой не оказалось в шкафу с инструментами на рабочем месте, а обнаруживалось это уже после запуска станка.
Внедрили стандартизацию процессов
Стандартизация процессов, по сути, входит в систему 5С, но хотелось бы остановиться на ней отдельно. Мы ввели несколько стандартов, касающихся непосредственно производства: «Заточка резца», «Подвод резца к валку на станке», «Отрезка прибылей», «Подготовка валка под УЗК», «Урезка бочки валка» и так далее.
Каждая рабочая операция была прописана максимально точно, что исключает двойные толкования и самодеятельность. Это значительно повысило качество работы и снизило количество брака, а значит, увеличило объем выпускаемой качественной продукции. Всю информацию о стандартах, регламентах, ходе работы участка любой сотрудник мог получить в информационном центре, организованном в цехе. Это особенно важно при сменном характере работы, кроме того, такая производственная информационная точка облегчает адаптацию новых сотрудников.
Изначально к внедрению новых регламентов и принципов работы сотрудники отнеслись настороженно, однако со временем работники цеха сами подключились к этому процессу.
Люди поверили. И практически все станочники активно участвовали в процессе, давали предложения по улучшению организации своих рабочих мест, — рассказывает Дмитрий Шавриков.
Результат:
- Время протекания производственных процессов сократилось с 192 до 145 часов;
- запасы незавершенного производства уменьшились на 30%;
- ежемесячная норма выработки на человека выросла с 15 до 17,2 тонн (в масштабе цеха, в котором работают 76 станочников, прирост равен152 тоннам в месяц);
- повышение производительности труда только на одном участке позволит в будущем году на имеющихся мощностях выпустить на 20% больше продукции.
За месяц цех обеспечил серьезный прирост и превысил 1400 тонн выработки. Это железный аргумент за то, чтобы и дальше двигаться, не останавливаться, чтобы был постоянный результат. Это важно, — заявил директор по производству и перспективному развитию КЗПВ Радий Гималетдинов. По его словам, такого результата у вальцемеханического цеха еще не было.
Для достижения подобных результатов не потребовалось ни сколько-нибудь серьезных инвестиций, ни увеличения штата, ни длительного времени: проект занял около пяти месяцев. В дальнейшем планируется распространить принципы стандартизации процессов и бережливого производства на других участках производства: шлифовки, фрезеровки, чистовой обработки, а также внедрить планово-предупредительные ремонты.
Что такое нацпроект «Производительность труда и поддержка занятости» и как принять в нем участие?
- работают в сфере обрабатывающих промышленных производств, транспортного, строительного, сельскохозяйственного секторов и отрасли ЖКХ;
- получили за последний год от 400 млн руб. до 30 млрд руб. выручки;
- имеют уставной капитал, в котором доля участия налоговых резидентов иностранных государств не превышает 25%.
Чтобы принять участие в программе, необходимо оставить заявку на сайте производительность.рф.