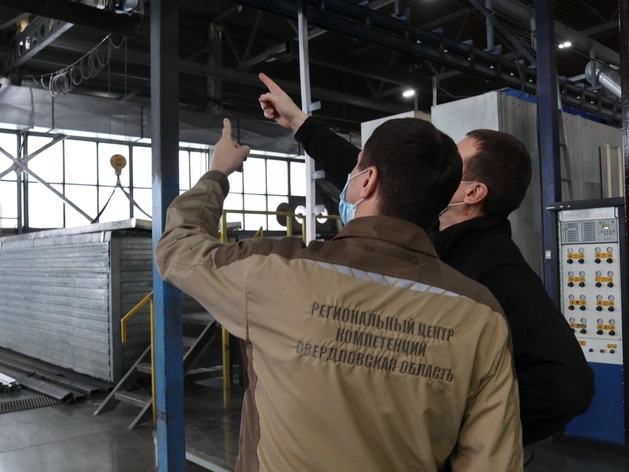
В Свердловской области полным ходом идет реализация национального проекта «Производительность труда». В среднем участникам удается увеличить выработку более чем в 1,5 раза.
DK.RU и Региональный центр компетенций (РЦК) продолжает цикл публикаций об успехах предприятий Свердловской области в рамках реализации нацпроекта «Производительность труда». Надо отметить, что на территории региона программа идет опережающими темпами. К 2021 г. планировалось заключить договоры участия с 74 предприятиями области, но на текущий момент их уже 87. До 2024 г. участниками нацпроекта станут 297 компаний.
К реализации программы эксперты РЦК и ФЦК (Федерального центра компетенций, прим.ред.) приступили еще на семи предприятиях: Уральском металлургическом заводе, Бобровском изоляционном заводе, ООО «Бурильные трубы», АО «СУЗМК ЭНЕРГО», Производственном предприятии электроавтоматики СИВАР, кирпичном заводе «Стройпластполимер» и Механо-литейном заводе. На производствах проведено обучение основам бережливого производства, а руководящий состав заводов готовится к реализации проекта по повышению производительности труда.
«В Свердловской области национальный проект реализуется успешно, ярко. Все участники достигают серьезных показателей роста производительности. В среднем за полгода объемы выпуска продукции увеличиваются на 20%, а снижение времени изготовления составляет порядка 40%. И принципиально важно: мы видим очередь из предприятий в проект, а значит, в регионе инициативу Президента поддерживают и бизнес, и власть», — отмечает Николай Соломон, генеральный директор Федерального центра компетенций.
Время протекания процесса сократили на 10 суток
В конце 2020 г. к участию в нацпроекте «Производительность труда» присоединилась Урало-Сибирская профильная компания (УСПК). Предприятие занимается разработкой инновационных и надежных решений из алюминия для современного строительства.
Фото: Урало-Сибирская профильная компания
Эксперты РЦК выявили главную проблему предприятия — несовершенную систему изготовления продукции. Дело в том, что весь материальный поток предприятия проходил через склад, и время протекания процесса составляло 20 дней. В качестве потока-образца была выбрана линия изготовления строительного системного профиля, которая приносит предприятию 40% от всей выручки.
«На этапе производственного аудита эксперты РЦК выяснили: если продукцию завода не везти на склад, а транспортировать сразу по технологическим переделам, можно сократить время протекания процесса до 10 суток. В два раза! Теория была уже проверена опытным путем. Со склада шла только доукомплектация неходовых позиций», — рассказывает руководитель проекта РЦК на УСПК Сергей Васюк.
Работа «в обход» склада позволила ускорить и другие технологические процессы на предприятии. Так, на прессование продукции стали уходить сутки, на термообработку — сутки, два дня — на покраску и два дня на упаковку товара. Раньше те же процессы занимали в два раза больше времени, и все из-за ожидания комплектации со склада следующих переделов.
Фото: Урало-Сибирская профильная компания
Надо отметить, что к нововведениям, предложенным специалистами Регионального центра компетенций, в Урало-Сибирской профильной компании отнеслись не просто с пониманием, а с воодушевлением.
«Сотрудники УСПК активно включились в работу по модернизации основных процессов предприятия, прошли специальное обучение, где им рассказали о главных принципах бережливого производства. Положительным результатом этой стартовавшей трансформации для нас будет увеличение производительности на 30%. Для достижения таких показателей нам потребуется год-два», — говорит Евгений Хадасевич, директор по производству УСПК.
Работы по повышению производительности труда на УСПК еще не закончены. Следующие три месяца новая схема работы будет оттачиваться. Кроме того, изменения необходимо будет внести в информационную систему — это задача программистов.
Фото: Урало-Сибирская профильная компания
В новой системе планирования будут выдаваться сменные задачи с передела на передел и отслеживаться запасы продукции, хранящиеся уже не на складе, а в специальных буферных зонах, — резюмирует Сергей Васюк.
Выработка изделий увеличена почти в два раза
Полугодовой цикл работ экспертов РЦК недавно завершился на Первоуральском заводе комплектации трубопроводов (ПЗКТ). Основные мероприятия проходили на участке №2, где изготавливаются крутоизогнутые отводы диаметром 273-820 мм. Здесь наблюдалось большое количество незавершенного производства, необходимо было сокращать производственный цикл и оптимизировать работу сотрудников.
Фото: Первоуральский завод комплектации трубопроводов
«Команда ПЗКТ прошла обучение. Нам дали основы бережливого производства, знания о том, что такое 5С на производстве, научили применять картирование потока и анализировать эффективность оборудования», — рассказывает технолог ПЗКТ Дмитрий Барышев.
После проведенного аудита эксперты РЦК разработали систему мероприятий, которые позволили предприятию достичь существенных улучшений. В частности, было решено проводить ежемесячный обход участка, чтобы отслеживать порядок на местах, в системах хранения и состояние оборудования. Сократить производственные потери помогло внедрение технологии 5С на производстве, а также снижение затрат на вспомогательные операции.
Фото: Первоуральский завод комплектации трубопроводов
Отдельный блок работ был посвящен производственному анализу: на предприятии внедрили почасовой контроль выполнения сменных заданий, причины отклонений фиксировались в специальном бланке.
«После проведения основного цикла мероприятий фактические производственные показатели приблизились к идеальным. За счет синхронного запуска производства в потоке увеличена выработка изделий на час в смену почти вдвое — с 1,75 до 3,3 штук. Благодаря сокращению перемещений и ожиданий в потоке от склада сырья до склада готовой продукции время изготовления партии продукции сократилось более чем в два раза — с 22,7 дней до 11-ти. За счет снижения партии передачи заготовок между переделами и определения минимальных и максимальных остатков на складе готовой продукции незавершенное производство в потоке удалось сократить с 1040 до 144 штук деталей», — делится результатами полугодовой работы Андрей Максимов, руководитель проекта РЦК на ПЗКТ.
Фото: Первоуральский завод комплектации трубопроводов
Федералы на Урале
Помогают повышать производительность труда уральским предприятиям не только эксперты РЦК, но и сотрудники Федерального центра компетенций.
Так, компании «Росэнерготранс» совместно с экспертами ФЦК в процессе оптимизации производства сухого трансформатора удалось сократить время протекания процессов с 416 до 240 часов — на 42%. Запасы незавершенного производства в потоке уменьшились с 95 до 70 штук, а выработка выросла на 25%.
«На производстве было выявлено пять основных проблем: большие запасы, неравномерная загрузка участков, перепланирование, некорректные остатки, большая загрузка начальников участков. Для их решения мы создали виртуальный склад для хранения. Это позволило устранить потери времени поиска необходимых комплектующих. Совершенствование системы планирования позволило оптимизировать размер производственных запасов. Кроме того, мы снизили простои по отсутствию деталей, тем самым увеличили производительность производства: сборка деталей на потоке-образце до нашего появления на предприятии составляла 289 минут, а стала 190», — рассказывает эксперт ФЦК по проекту «Росэнерготранс» Сергей Шурыгин.
Более эффективным представители ФЦК помогли стать и Уральскому заводу трубной изоляции (УЗТИ). Время протекания процессов здесь было сокращено на 40% — со 109 до 65 часов, а выработка увеличена почти в 3 раза — с 33 до 93 погонных метров в час. В качестве потока-образца эксперты ФЦК выбрали участок ППУ изоляции. Перепланировка участка позволила освободить более 200 м2 производственных площадей. Подтвержденный экономический эффект на этапе совместной работы с экспертами ФЦК составил 80 млн руб.
«Мы создали систему обеспечения рабочих мест комплектующими. Это позволило сократить время протекания процесса на 125 минут. Была организована система супермаркетов входящих комплектующих. Надо отметить, что Уральский завод трубной изоляции — перспективное предприятие. Он заинтересован в улучшениях и применяет сейчас принципы бережливого производства не только непосредственно на производственных мощностях, но и в офисе. По-другому выстраивается работа с менеджерами по продажам и обеспечение их необходимыми материалами. Развитие этого предприятия уже не остановить», — отмечает Григорий Клячев, эксперт ФЦК по проекту УЗТИ.
Как принять участие в нацпроекте «Производительность труда»
Предприятия, желающие стать частью национальной программы, должны соответствовать следующим параметрам:
- Работать в области обрабатывающих промышленных производств, транспортного, строительного, сельскохозяйственного секторов.
- Выручка компании за последний год должна составлять более 400 млн руб.
- Доля участия налоговых резидентов иностранных государств в уставном капитале не должна превышать 25%.
Нацпроект будет реализовываться до 2024 года. Заявки на участие принимаются на сайте производительность.рф.
Больше материалов о бережливом производстве на DK.RU:
«Повышаем производительность — растет зарплата». Зачем уральские заводы идут в нацпроект
Переставили станки — и поставили личный рекорд. Разбираем кейс оптимизации производства
«Главное — вовремя задать нужный вопрос». Как повышать производительность без инвестиций
Главное — тесная связка с людьми. Как уральский завод в три раза ускорил производство
Материалы по этой теме: #СПЕЦПРОЕКТЫ #ПРОИЗВОДИТЕЛЬНОСТЬ ТРУДА #БИЗНЕСПодписывайтесь на DK.RU в Дзен и Дзен.Новости. Самое важное о бизнесе — в email-рассылкe. А еще нас удобно читать в Telegram и ВКонтакте.