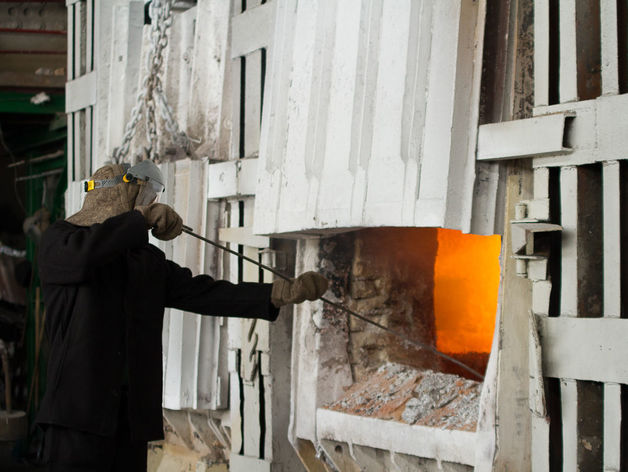
Считается, что экспортеры сейчас чувствуют себя уверенно и устойчиво. DK.RU побывал на предприятии, признанном лучшим экспортером Свердловской области. Фоторепортаж с уникального производства.
Компания «Сеал и К» производит алюминиевые сплавы. Особенность в том, что алюминий она добывает из вторичного сырья — отходов с других предприятий, бытового и промышленного лома. Технология эта уникальна, в России работают не более трех подобных установок. Среди конечных потребителей продукции — Honda, Toyota, Mitsubishi и др.
Конкурс «Лучший экспортер Свердловской области» для предприятий малого и среднего бизнеса был проведен в этом году впервые. Организаторы — министерство инвестиций и развития Свердловской области и областной фонд поддержки предпринимательства.
Основными критериями отбора были объем и география экспорта, наличие международных сертификатов и наград. У победителя — «Сеал и К» экспорт занимает 90% валовой продукции. У лауреатов конкурса этот показатель ниже — так, производитель фанеры «Эко-групп» (2-е место) отправляет за границу 60-70% продукции, а занимающееся деревообработкой ИП Козьменко И.С. (3-е место) продает в другие страны 52% пиломатериала.
Компания «Сеал и К» начала работать в пос. Монетный в 1997 г. До этого у нее было маленькое производство на Сухоложском заводе цветных металлов.
«Мы специально искали цеха, где можно было сразу начинать работаь, — рассказывает исполнительный директор ООО «Сеал и К» Григорий Герцберг. — До нас здесь был Монеткинский опытный металлургический завод, занимался он литейкой и обработкой черных металлов. Когда мы его купили, здесь почти ничего не оставалось, только стены цехов, да и то не везде. Все, что не продали арбитражники, вынесли остальные. Все, что можно было снять, было снято. Дорог не было никаких, люди, когда начинался завод, приходили на работу в болотниках. Так что и ливневую канализацию, и дороги внутри и на подъезде к заводу — делали мы сами».
Асфальтировали внутреннюю территорию своими силами
Для изготовления сплавов используются три вида сырья: лом, стружка и шлак. Стружка и шлаки — приходят с металлургических предприятий (КАМАЗ, АвтоВАЗ, группы РУСАЛ, Каменск-Уральский металлургический завод, Самарский метзавод). А лом — это то, что образуется у населения или у крупных промпредпритяий в процессе обработки деталей.
Различные виды алюминиевого лома
Лом сортируется, прессуется и измельчается в специальной дробилке
«20-25 лет назад шлаки, образующиеся в процессе производства алюминия, вообще не перерабатывались, — рассказывает Григорий Герцберг. — Их просто закидывали в яму и зарывали. Потом появилась технология, которая позволяла извлекать из этих шлаков оставшийся алюминий. В России таких установок, которые этим занимаются, можно пересчитать по пальцам одной руки. Я знаю только одну помимо нас, которая действует».
Шлак, который приходит от крупных производителей алюминия
Смешивать шлак от разных партий и предприятий нельзя — он весь отличается по химическому составу, металлургическому выходу (содержанию алюминия), фракционному составу. Поэтому пробы с каждой партии отправляют в лабораторию и анализируют. Эти данные помогают определить оптимальную схему переработки шлака.
Сырье отправляется на участок подготовки шлака, созданному по аналогу испанской фирмы «Реметалл». Большая часть оборудования привезена из Европы, есть и российское. Здесь происходит многоступенчатое дробление, измельчение, грохочение, электромагнитная сепарация шлаков. На выходе получается обогащенный алюминиевый концентрат, с 50%-ным содержанием алюминия. Последующая задача — этот алюминий в процесс переплавки извлечь.
Участок подготовки шлака, на нем работают пять человек.
Готовый концентрат по транспортерам поступает в металлургический цех.
Большая часть плавильной системы — газогорелочное устройство, гидравлика, частично механизм — была привезена из Италии. Но металлоконструкцию самой печи по чертежам изготовили на Уралмашзаводе: экономически неоправданно везти такой вес из Италии.
Расплавленный металл стекает в миксеры, где обогащается в зависимости от того, какой в данный момент сплав готовится: в него добавляют кремний, медь и т.д. В процессе можно снимать пробы.
После того как будет готов нужный сплав, бочка поднимается и металл разливается по формам. В день можно отливать порядка 55 тонн.
«Если вы в этом году купили американскую машину, то, возможно, запчасти в ней отлиты из наших сплавов. А если в прошлом году вы покупали Volkswagen, то с большой долей вероятности ваш мотор — из Монетного», — говорит Григорий Герцберг.
Вторичные сплавы отличаются друг от друга содержанием элементов. Мировые автоконцерны закупают здесь металл, из которого потом отливают двигатели и запчасти. Требования у них очень высокие: попадать нужно в сотые доли процентного содержания элементов. Самый сложный сплав — тот, из чего льют автомобильные диски. «Сеал и К» производит 20 тонн такого сплава в месяц. Это много: в среднем диск весит 3 кг.
Григорий Герцберг: «Это один из самых дорогих сплавов, его безумно тяжело производить. Когда мы отливаем его, весь завод стоит на ушах».
Сложность при отливе сплава для дисков — точное соблюдение химического состава. В алюминии есть примеси: медь, железо, цинк, магний, кремний, свинец, олово. И каждый должен попадать в определенную грань, в десятые, сотые доли процента. Например, на выходе все элементы должны быть по 0,001, 0,5 и т.п., кроме кремния — его должно быть строго 11%. Добавлять кремний тяжело: насыщаешь сплав кремнием, а во время отливки из-за кремния чушка начинает ломаться. И нужно медленно, понемногу подавая капельки воды, удерживая поверхность, отливать этот сплав.
На этом участке отливаются и упаковываются чушки, из которых позже сделают автомобильные моторы
Вся продукция вывозится по собственным железнодорожным путям
В планах компании — расширить не только линейку сплавов, но и найти более эффективное применение территории завода. Сейчас ведется поиск арендаторов, которые смогут используя инфраструктуру, заниматься здесь смежной деятельностью.
Фото: Игорь Черепанов, DK.RU
Подписывайтесь на DK.RU в Дзен и Дзен.Новости. Самое важное о бизнесе — в email-рассылкe. А еще нас удобно читать в Telegram и ВКонтакте.