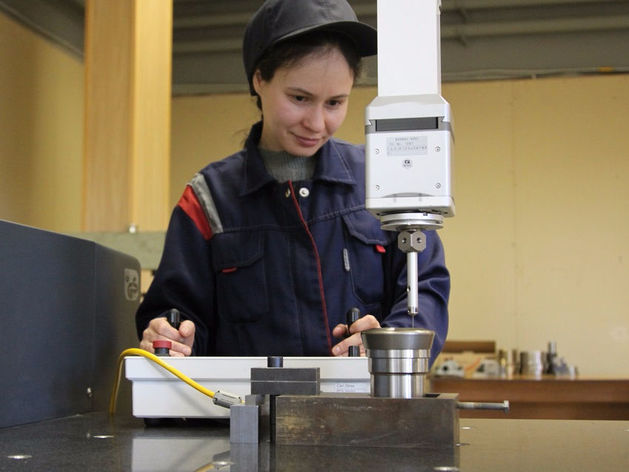
Импортозамещение – одно из главных направлений стратегии развития дивизиона «Сортовой прокат Россия» Группы НЛМК.
Предприятия дивизиона расширяют использование отечественных материалов, программного обеспечения, инструментов и создают качественные аналоги импортной продукции. Работа по импортозамещению ведется на НЛМК-Урал Сервис, который обеспечивает НЛМК-Калуга, НЛМК-Метиз и НЛМК-Урал необходимыми запасными деталями и расходными материалами для импортного оборудования.
Курс на отечественную продукцию сотрудники НЛМК-Урал Сервис взяли еще в 2005 году, когда завершилась большая реконструкция на НЛМК-Метиз. Завод был переориентирован на производство метизной продукции, закупили новейшее европейское оборудование. Тогда специалисты НЛМК-Урал Сервис впервые приступили к освоению технологий изготовления запчастей для импортного оборудования. Выпустили накатные плашки для производства саморезов и холодновысадочные инструменты, полностью отвечающие зарубежным образцам.
Сегодня НЛМК-Урал Сервис создает комплектующие разной степени сложности для оборудования прокатного, метизного и сталеплавильного производства. Форсунки, регистры, привалковую арматуру, детали для кранового оборудования, гвоздильный инструмент – в 2016 году НЛМК-Урал Сервис изготовил более 4000 изделий взамен импортных деталей.
«В настоящее время мы работаем над двумя проектами для НЛМК-Калуга, осваиваем изготовление панели горелки дуговой сталеплавильной печи. В работе опытная партия - четыре штуки. Это нестандартные специфические изделия с повышенными требованиями к герметичности, необходимые для сварных соединений сталь-медь. Также сейчас в производстве партия кантующих роликов для сортопрокатного производства НЛМК-Урал и НЛМК-Калуга», – говорит Виталий Токарев, начальник производственного цеха.
По словам Виталия Токарева, на изготовление одной детали уходит в среднем около 30 дней в зависимости от сложности изделия.
Все начинается в производственно-технологическом отделе, где инженеры-конструкторы и технологи разрабатывают конструкторскую и технологическую документацию, а также выбирают материалы, необходимые для будущего изделия.
Дальше за дело берутся сотрудники инструментального участка производственного цеха. Над созданием новой продукции работают инженеры и операторы станков с программным управлением.
«Благодаря большому разнообразию высокоточного оборудования мы можем изготавливать очень широкую номенклатуру деталей и запасных частей для металлургического и метизного производства», – рассказывает начальник инструментального участка Леонид Кудрявцев.
Рассмотрим, как создают новую продукцию на примере детали вязальной головки. Ее изготавливают для прокатного стана 250 в Нижних Сергах. В январе на НЛМК-Урал Сервис произвели опытную партию вязальных головок. Сейчас персонал работает над резервной партией.
«Первое, с чего начинается изготовление – черновая обработка на токарном станке с числовым программным управлением, – рассказал Леонид Кудрявцев. – Здесь деталь во время вращения обрабатывается резцом, снимающим слой металла с поверхности заготовки. Это позволяет достичь полного соответствия необходимому диаметру будущего изделия».
После этого деталь отправляется на фрезерный обрабатывающий центр, где выполняется наиболее сложная и ответственная часть работы – обработка сложных криволинейных поверхностей, которые выполнить на обычном фрезерном станке невозможно.
Для придания детали необходимой твердости и прочности производится термическая обработка в вакуумной печи.
Затем изделие вновь возвращается на токарный станок с программным управлением для чистовой обработки, где вносятся последние штрихи. Чистовая обработка позволяет достичь требуемой точности, уменьшает неровности, шероховатости, улучшает эксплуатационные характеристики изделия.
Завершающим этапом становится обработка на электроэрозионном прошивочном станке, где прожигаются пазы, имеющие высокую степень точности.
В финале для контроля качества и соответствия детали необходимым геометрическим параметрам, указанным в чертеже, вязальная головка поступает на контрольно-измерительную машину. Инженер проводит измерения готового изделия и выдает протокол о соответствии всем параметрам. И деталь отправляется на склад готовой продукции.
Дмитрий Стопкевич, генеральный директор НЛМК-Сорт:
Освоение производства запасных деталей на НЛМК-Урал Сервис стало жизненной необходимостью – благодаря этому мы обеспечиваем нужными деталями наши предприятия в Березовском, Нижних Сергах и Ревде. Теперь мы можем предложить высококачественную продукцию и сервис не только нашим предприятиям, но и сторонним заказчикам.
Информация об НЛМК-Сорт:
Предприятия НЛМК-Сорт - одни из крупнейших производителей сортового проката и метизной продукции на российском рынке. НЛМК-Сорт входит в Группу НЛМК.
В состав дивизиона входят предприятия: НЛМК-Урал, НЛМК-Метиз, НЛМК-Калуга, НЛМК-Урал Сервис и Вторчермет НЛМК. Таким образом, производственная структура НЛМК-Сорт включает мощности, образующие замкнутый производственный цикл от сбора и переработки лома черных металлов до выпуска металлургической продукции высоких переделов – арматурного проката, катанки и метизов.
Производственные мощности дивизиона «Сортовой прокат Россия» Группы НЛМК позволяют выпускать до 3,7 млн т/г стали, 2,9 млн т/г арматурного проката и катанки, направляемой как на реализацию, так и на дальнейший передел на собственном метизном производстве мощностью 0,5 млн т/г.
Общая численность персонала составляет более 9 тыс. человек.
Страница НЛМК-Урал Сервис.
Подписывайтесь на DK.RU в Дзен и Дзен.Новости. Самое важное о бизнесе — в email-рассылкe. А еще нас удобно читать в Telegram и ВКонтакте.